5 Signs Your Manufacturing Equipment is Headed for Failure


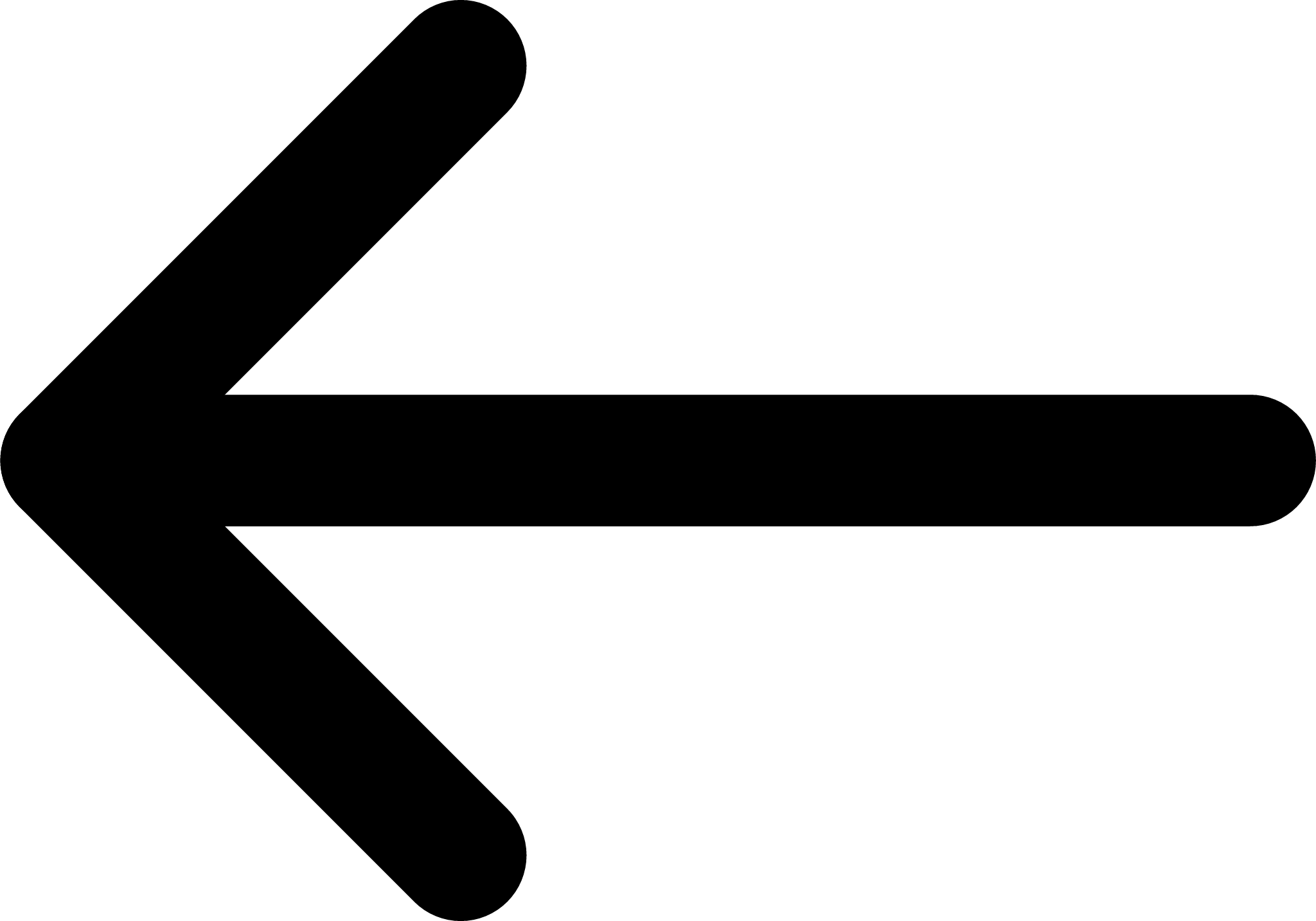
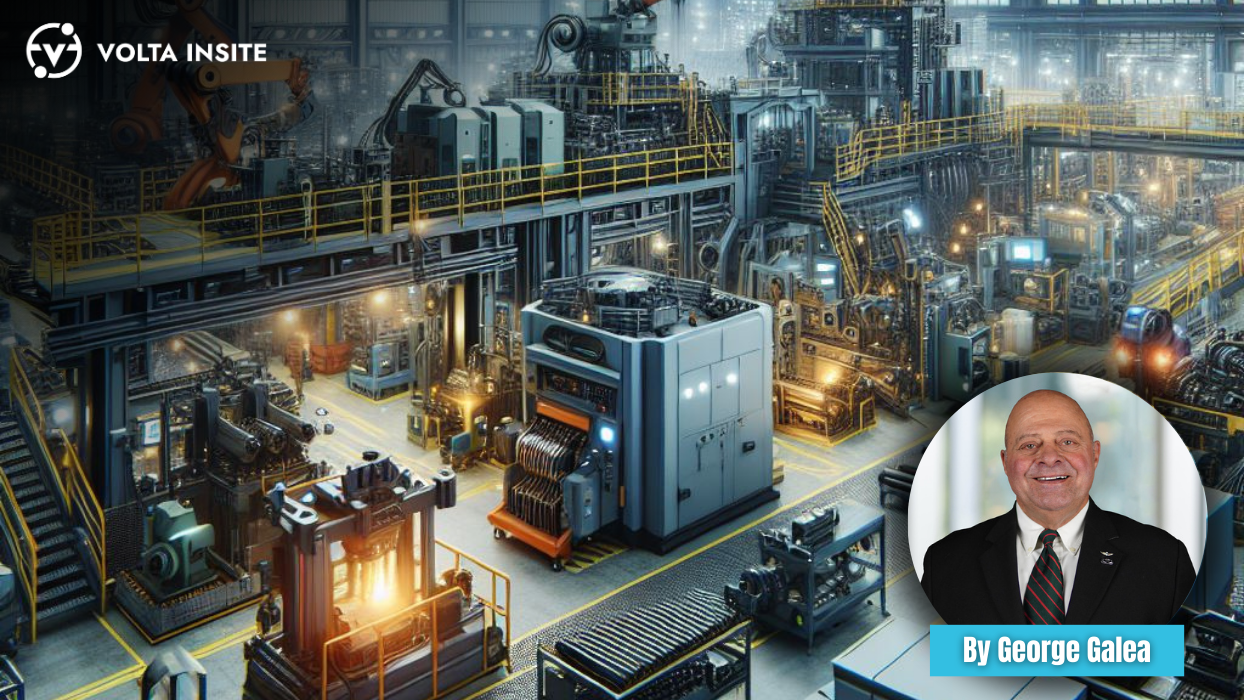
Equipment failure in manufacturing can lead to costly downtime, missed production targets, and expensive emergency repairs. However, most failures don’t happen without warning. Subtle changes in performance, efficiency, and condition often signal that a breakdown is on the horizon. Identifying these warning signs early allows for proactive maintenance and prevents unexpected disruptions.
Here are five key indicators that your manufacturing equipment may be on the verge of failure—and what you can do to prevent it.
1. Unusual Noises and Vibrations
A well-maintained machine runs smoothly with minimal noise. If you start hearing grinding, knocking, screeching, or excessive vibration, it could indicate:
-
Loose or worn-out components
-
Misalignment of moving parts
-
Bearing failure
-
Imbalance in rotating machinery
What to Do:
Don’t ignore unusual sounds. Conduct an inspection to pinpoint the source of the issue. Using vibration analysis tools can help detect misalignment or bearing wear before they lead to catastrophic failure.
2. Increased Energy Consumption
If your equipment is suddenly using more power than usual, it could signal:
-
Motor inefficiencies
-
Overheating components
-
Blocked airflow in cooling systems
-
Electrical faults
What to Do:
Monitor energy usage regularly. A sudden spike in power consumption should prompt an inspection of motors, electrical components, and cooling systems. Thermographic imaging can also help identify overheating parts.
3. Frequent Overheating
Excessive heat is a major red flag that machinery is under strain. This could be due to:
-
Poor lubrication
-
Cooling system failure
-
Excessive friction in moving parts
-
Electrical overloads
What to Do:
Check lubrication levels, airflow, and electrical loads. Infrared thermal scanning can help detect hot spots before they cause serious damage.
4. Declining Performance and Inconsistent Output
If a machine is producing defective products, slowing down, or struggling to maintain speed, it may be due to:
-
Worn-out components
-
Control system malfunctions
-
Mechanical degradation
What to Do:
Conduct regular performance tests and compare results against baseline efficiency data. If output quality is dropping, a deeper inspection is needed to identify worn or failing parts.
5. Unexplained Leaks or Fluid Loss
Leaks in hydraulic systems, coolant lines, or lubrication systems often indicate:
-
Seal or gasket failure
-
Hose deterioration
-
Internal pressure imbalances
What to Do:
Inspect hoses, seals, and fittings regularly. A minor leak can escalate into a major system failure if left unchecked.
How Predictive Maintenance Can Help
While these warning signs can be caught through routine inspections, predictive maintenance takes failure prevention to the next level. By leveraging real-time sensor data, AI-driven analytics, and IoT monitoring, predictive maintenance detects potential failures before they become major problems.
Predictive Maintenance Benefits:
-
Detects wear and tear early with vibration, temperature, and power consumption tracking.
-
Reduces downtime by scheduling repairs before failures occur.
-
Improves efficiency by optimizing maintenance schedules based on real-time data.
-
Lowers repair costs by addressing small issues before they escalate.
Instead of waiting for failure to happen, Volta Insite’s predictive maintenance solutions help manufacturers stay ahead of equipment breakdowns. Contact us today to learn how we can help keep your production running smoothly.