The Best Spring Maintenance Checklist for Industrial Facilities


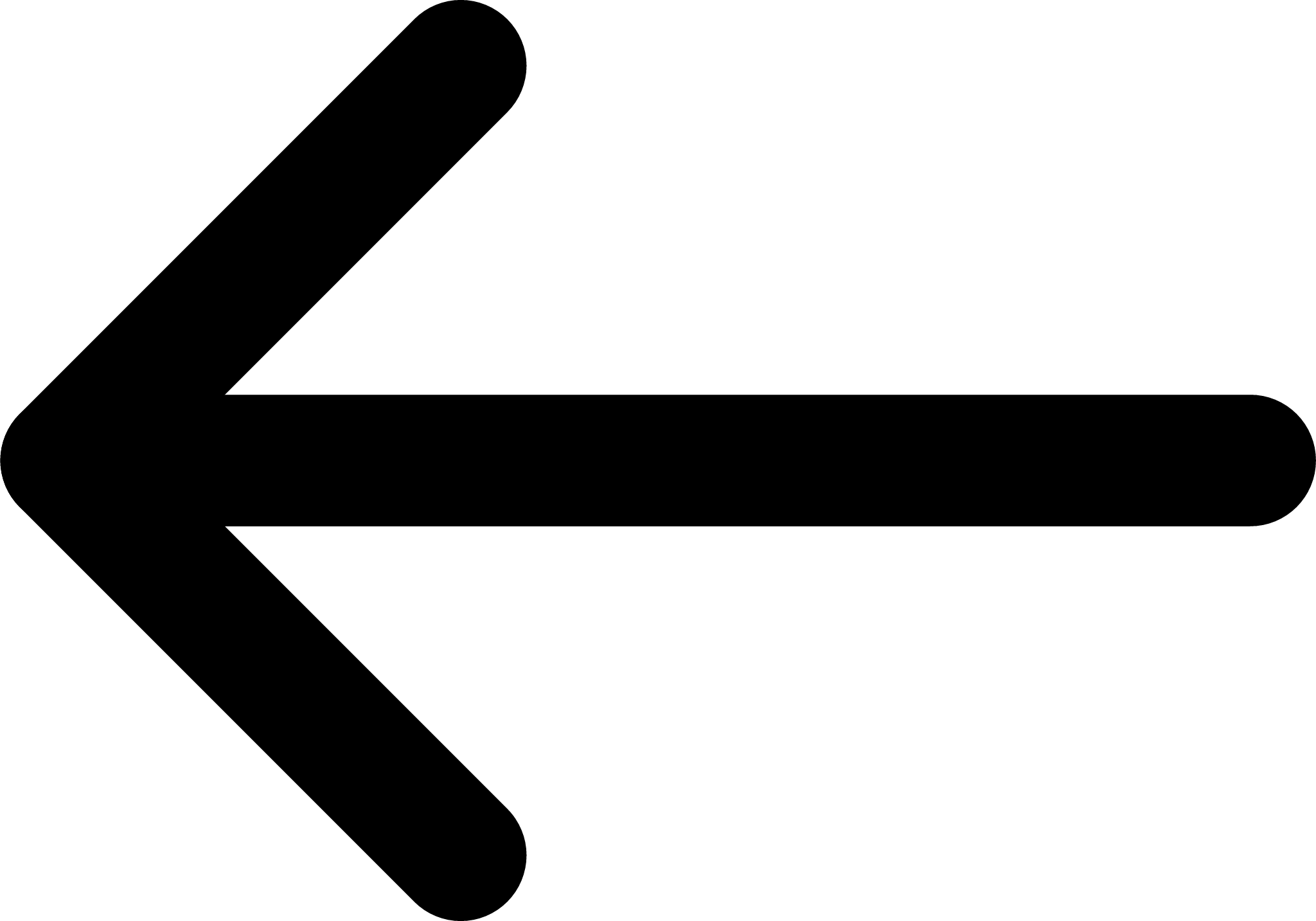
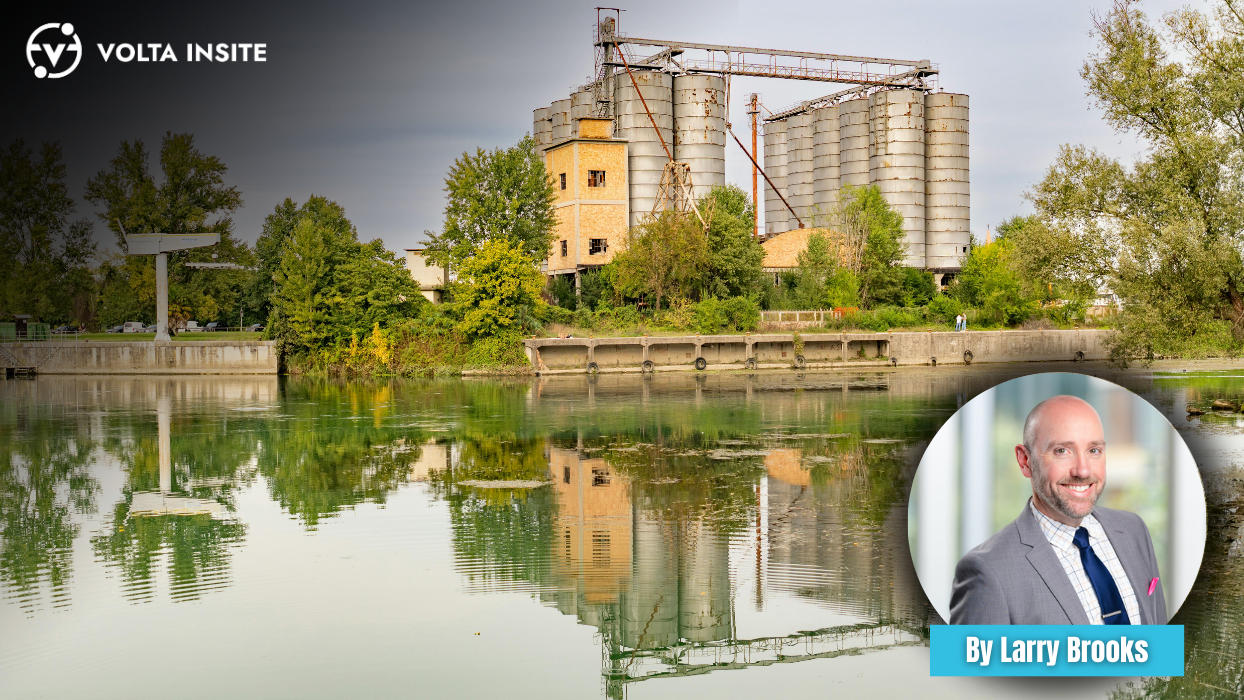
As temperatures rise, industrial facilities must prepare for the seasonal shift to ensure optimal equipment performance. Spring is the perfect time to assess systems, conduct preventive maintenance, and implement predictive strategies to prevent costly breakdowns. A well-structured maintenance checklist helps facilities reduce downtime, improve efficiency, and maximize equipment lifespan.
Here’s the ultimate spring maintenance checklist for industrial facilities to keep operations running smoothly.
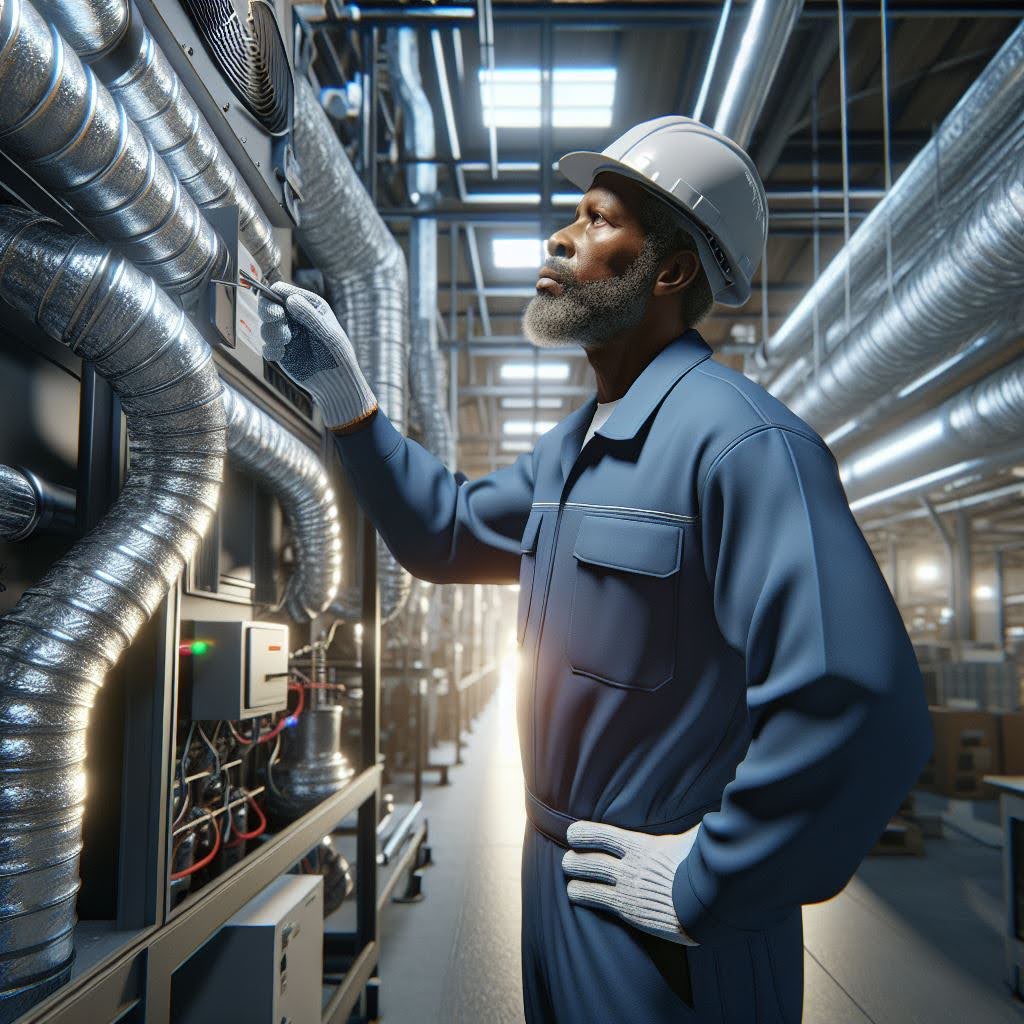
1. Inspect HVAC and Cooling Systems
With rising temperatures, HVAC systems work harder to regulate facility conditions. A poorly maintained system can lead to overheating, inefficiency, and unexpected failures.
-
Clean or replace air filters to improve air quality and efficiency.
-
Inspect ducts for leaks or blockages that could restrict airflow.
-
Check refrigerant levels to ensure optimal cooling performance.
-
Test system components, including thermostats and control panels.
2. Assess Electrical Systems and Backup Power
Spring storms can lead to power outages and electrical surges. A thorough inspection ensures your electrical infrastructure is prepared.
-
Test generators and backup power sources to confirm reliability.
-
Inspect circuit breakers, transformers, and wiring for signs of wear or overheating.
-
Ensure surge protectors and grounding systems are functioning properly.
3. Service Pumps, Motors, and Machinery
Machinery that sat idle or operated at reduced capacity during the winter may need servicing before ramping up production.
-
Lubricate moving parts to reduce friction and wear.
-
Inspect belts and chains for cracks, stretching, or misalignment.
-
Check hydraulic systems for leaks or pressure issues.
4. Conduct a Facility-Wide Safety Inspection
Spring is a great time to reinforce safety measures and conduct required inspections.
-
Test fire suppression systems, including alarms and sprinklers.
-
Inspect exits, lighting, and emergency pathways for compliance.
-
Check safety gear such as eyewash stations, harnesses, and PPE supplies.
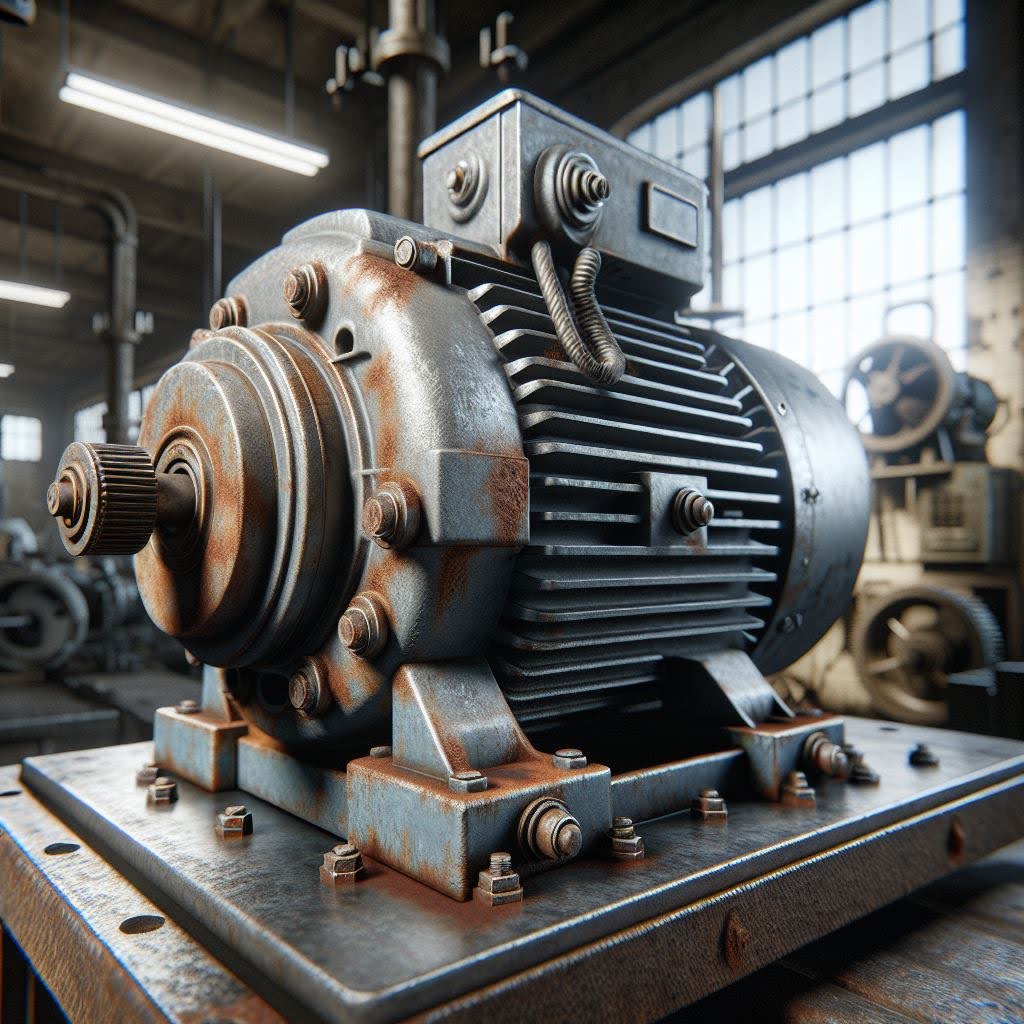
5. Prevent Rust and Corrosion in Equipment
Temperature fluctuations and humidity changes in spring can accelerate corrosion.
-
Apply protective coatings to exposed metal surfaces.
-
Inspect piping for leaks, rust, or mineral buildup.
-
Test water drainage systems to prevent standing water in critical areas.
6. Optimize Outdoor Areas and Drainage
Spring rain can create flooding hazards and drainage issues.
-
Clear gutters and storm drains of debris to prevent blockages.
-
Inspect parking lots and facility grounds for cracks or potholes.
-
Ensure proper grading to prevent water pooling near equipment or structures.
7. Implement Predictive Maintenance for Long-Term Success
While traditional maintenance checks help prevent immediate issues, predictive maintenance ensures long-term reliability. By using IoT sensors, AI-driven analytics, and real-time monitoring, facilities can detect potential failures before they happen.
-
Install condition-monitoring sensors to track vibration, temperature, and power usage.
-
Analyze performance data to predict when components need servicing.
-
Automate maintenance schedules based on real-time equipment health.
Spring Forward with a Smarter Maintenance Strategy
By following this spring maintenance checklist, industrial facilities can prevent costly failures, reduce downtime, and improve overall efficiency. Volta Insite’s predictive maintenance solutions help businesses stay ahead of breakdowns, ensuring smooth operations throughout the season. Contact us today to learn how predictive maintenance can transform your facility’s maintenance strategy!