Solving Dirty Power in Oil & Gas with Predictive Maintenance


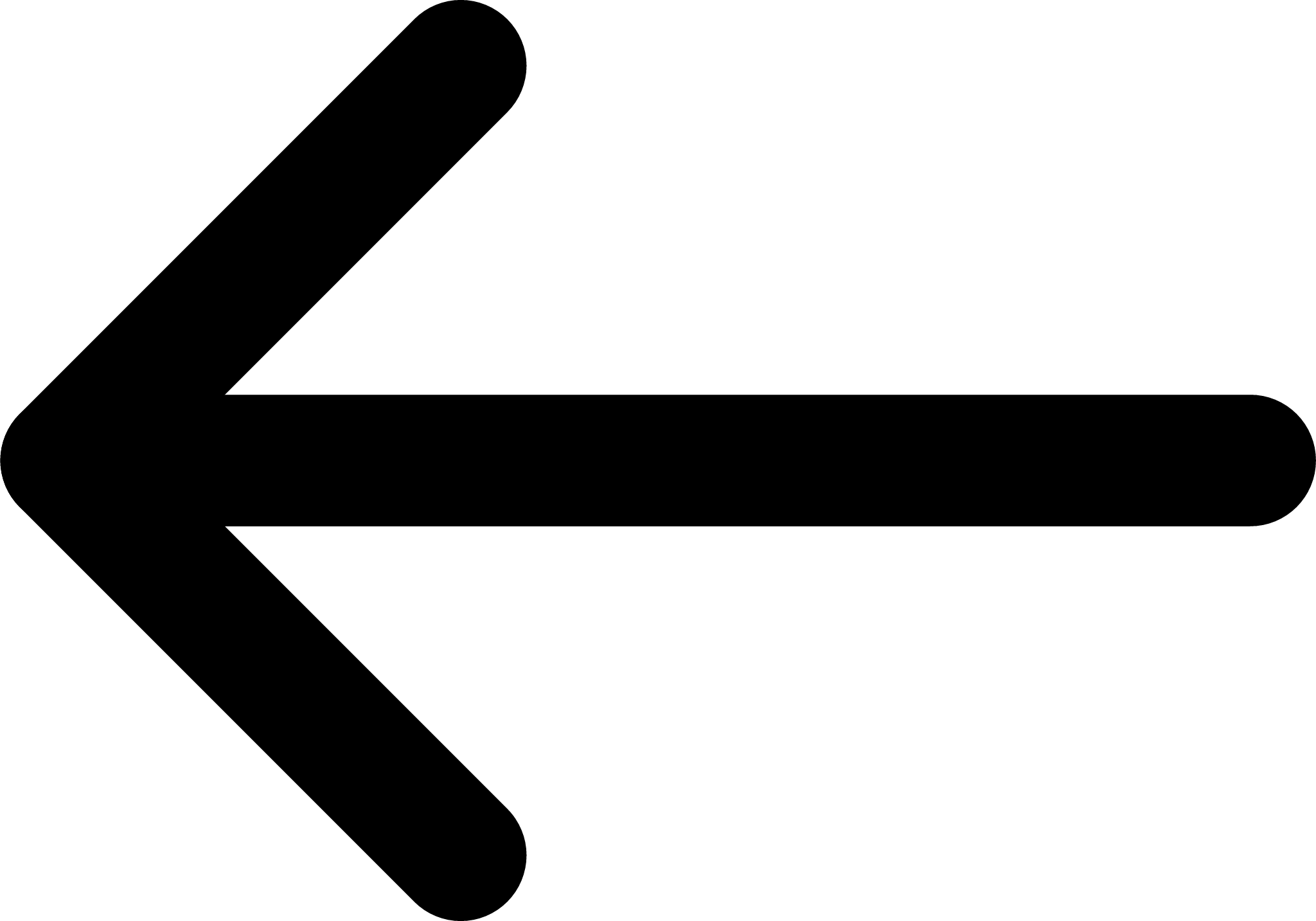
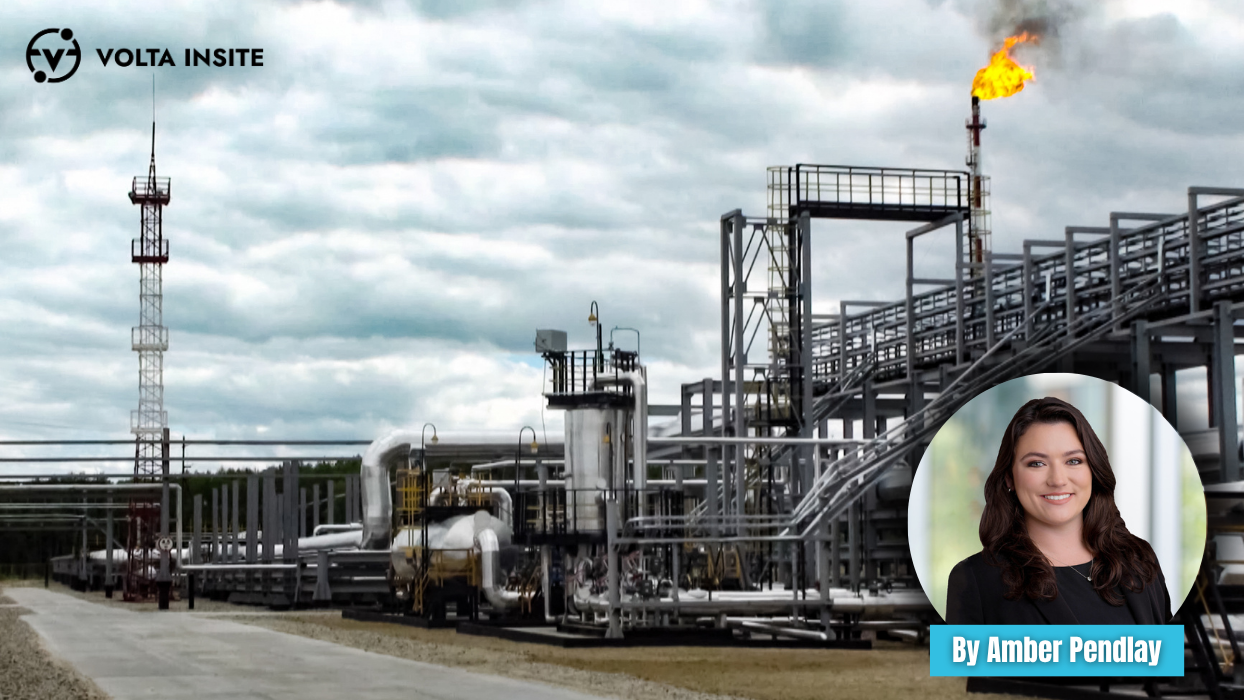
Unreliable power can be catastrophic in the oil, gas, and petrochemical industry. From upstream drilling rigs to downstream refining and chemical processing plants, every operation relies on a stable, high-quality power supply to maintain uptime, safety, and process efficiency. Yet, dirty power—electrical energy disrupted by harmonics, voltage imbalances, sags, swells, and transients—remains a widespread and costly issue.
For years, maintenance teams have dealt with dirty power reactively, troubleshooting after failures occur. But a new generation of AI-powered predictive maintenance tools is flipping the script—enabling oil and gas operators to detect power quality issues in real time, predict failures before they happen, and make data-driven decisions that reduce downtime, protect assets, and extend equipment life.
The High Cost of Dirty Power
Dirty power is often invisible—until it isn't. It manifests in unexpected equipment failures, nuisance trips, overheated motors, unplanned shutdowns, and excessive wear on electrical components. In a high-stakes industry like oil and gas, where equipment downtime can cost thousands of dollars per minute, these issues quickly escalate.
Some of the most common effects of dirty power include:
-
Transformer overheating
-
Variable frequency drive (VFD) faults
-
PLC and control system disruptions
-
Premature motor and generator failure
-
Increased maintenance intervals
-
Energy inefficiency and higher utility bills
Traditional maintenance practices, which rely on time-based inspections and manual diagnostics, often miss intermittent or transient power disturbances. And by the time a problem is identified, the damage may already be done.
Why Oil and Gas Facilities Are Especially Vulnerable
The oil, gas, and petrochemical industry presents unique electrical challenges:
-
Harsh, remote environments increase the risk of ground faults, poor grounding, and cable degradation.
-
Heavy use of VFDs and large motors makes systems more susceptible to harmonics and voltage instability.
-
Explosion-proof and safety-critical operations leave little room for error—especially when electrical failures can trigger shutdowns or hazards.
-
Aging infrastructure in many plants and platforms introduces further vulnerability to poor power quality.
In these environments, dirty power isn’t just a nuisance—it’s a safety and profitability risk.
A New Approach with AI-Powered Predictive Maintenance
Instead of waiting for dirty power issues to cause costly damage, AI-powered predictive maintenance provides constant, real-time visibility into power quality across an entire facility. These systems use smart sensors, high-frequency monitors, and edge computing to capture detailed electrical data—detecting even brief disturbances that would be missed by traditional tools.
Once collected, this data is analyzed by machine learning algorithms trained to recognize patterns of electrical degradation, component wear, and failure precursors. These systems can then:
-
Alert operators before a failure occurs
-
Correlate power events with specific equipment
-
Predict when and where maintenance is required
-
Track degradation trends over time
-
Optimize energy consumption and performance
Rather than relying on scheduled maintenance or reacting after an incident, facilities can act proactively, focusing efforts where they matter most.
Real-World Benefits for the Oil & Gas Sector
Facilities that adopt AI-driven predictive maintenance for power quality monitoring report significant benefits:
-
Reduced downtime by up to 50% through early issue detection
-
Extended equipment lifespan due to less electrical stress
-
Fewer unplanned shutdowns, which boosts safety and production
-
Improved compliance with NFPA, OSHA, and other safety standards
-
Energy cost savings through optimized electrical performance
In addition, historical data collected through AI tools supports root-cause analysis, enabling teams to prevent similar failures in the future.
Into the Future with InsiteAI by Volta Insite
For oil and gas operators looking to modernize their maintenance strategy, Volta Insite offers a proven solution: InsiteAI. This advanced platform combines real-time electrical monitoring with predictive analytics tailored to industrial environments—including upstream rigs, midstream compression stations, and downstream refining and petrochemical facilities.
InsiteAI empowers maintenance and reliability teams with:
-
Real-time insight into power quality across every panel
-
Predictive alerts for developing electrical issues
-
Trend analysis to guide long-term planning
-
Cloud-based dashboards are accessible from any location
-
Seamless integration with existing systems
By partnering with Volta Insite, oil and gas facilities gain more than just data—they gain actionable intelligence that helps them reduce risk, lower costs, and operate with greater confidence in power-critical environments.
Dirty power is an invisible threat that no oil and gas facility can afford to ignore. But with AI-powered predictive maintenance, identifying and correcting electrical issues before they escalate is no longer out of reach. Volta Insite’s InsiteAI is helping energy leaders take back control of their power quality—and their bottom line.