Difference Between Preventive & Predictive Maintenance


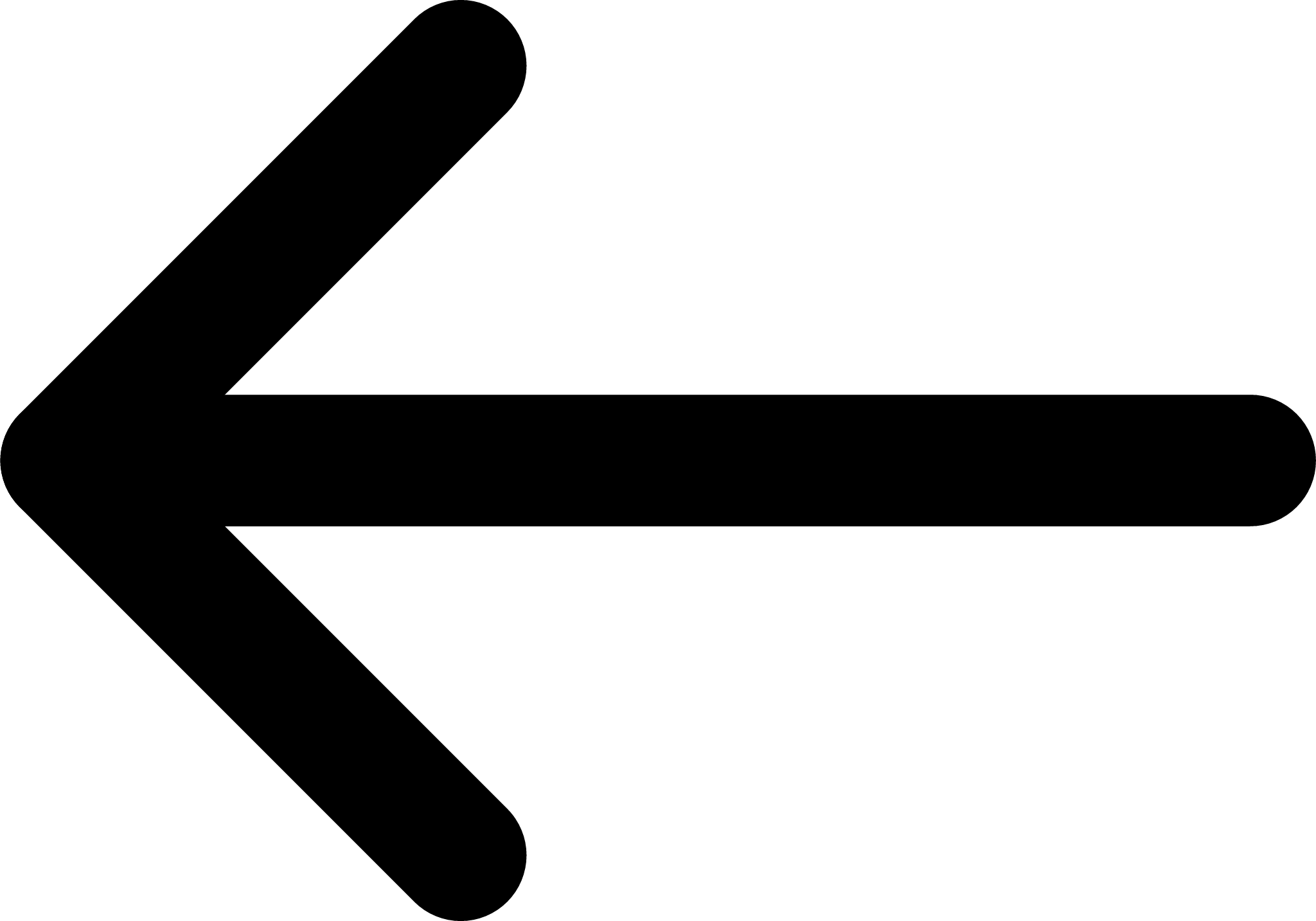
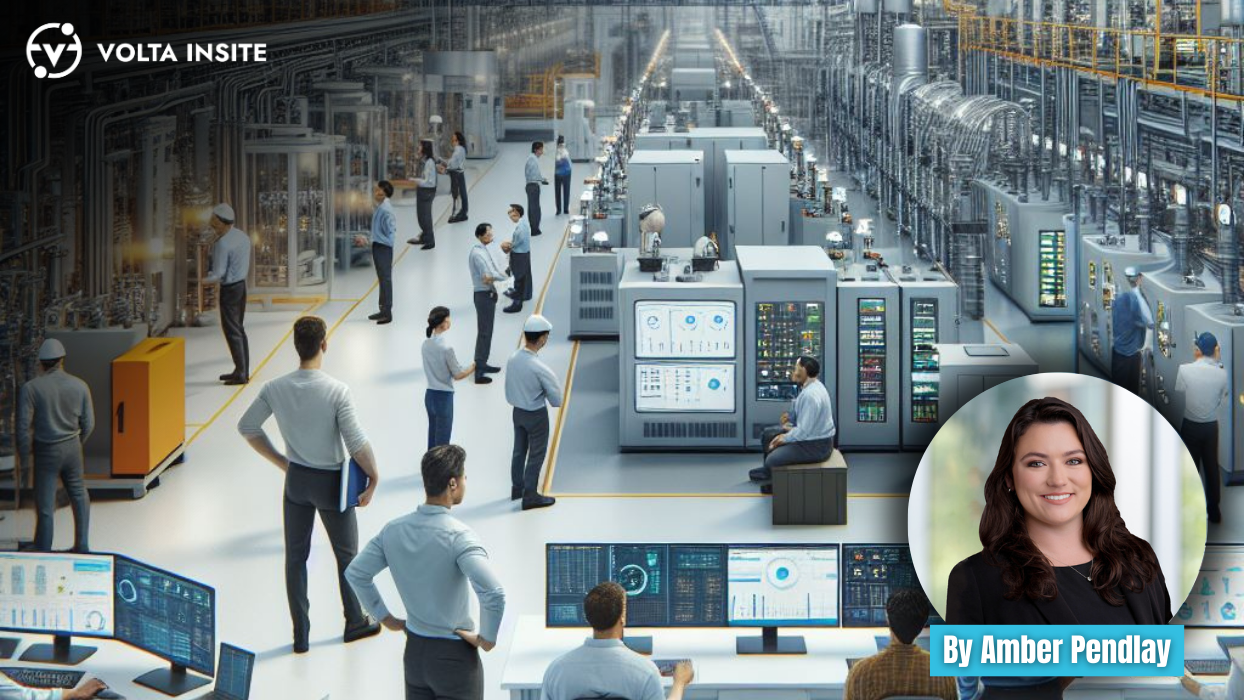
Facility management is undergoing a transformation. Traditional maintenance strategies, like preventive maintenance, have long been the standard for keeping equipment and infrastructure running. However, predictive maintenance is emerging as the more efficient, cost-effective, and intelligent approach to asset management. Understanding the differences between these two strategies is crucial for facility managers looking to improve operations, reduce costs, and extend equipment lifespan.
What is Preventive Maintenance?
Preventive maintenance follows a scheduled approach, where equipment is inspected, serviced, or replaced at predetermined intervals—whether or not an issue is present. This method aims to reduce unexpected failures and prolong asset life.
Common Preventive Maintenance Tasks:
-
Routine HVAC filter replacements
-
Periodic lubrication of mechanical components
-
Scheduled inspections of electrical systems
-
Timed replacement of parts based on manufacturer recommendations
While preventive maintenance helps avoid catastrophic failures, it has its drawbacks. Because it operates on a fixed schedule, unnecessary maintenance can occur, leading to wasted resources and increased downtime. Additionally, this approach doesn’t account for real-time conditions, meaning problems may still arise between scheduled maintenance cycles.
The Shift to Predictive Maintenance
Predictive maintenance leverages data-driven technologies like sensors, artificial intelligence, and real-time monitoring to assess equipment health continuously. Instead of relying on fixed schedules, predictive maintenance determines when servicing is actually needed based on performance trends and early warning signs of failure.
Key Benefits of Predictive Maintenance:
Real-Time Monitoring
Sensors track critical parameters such as temperature, vibration, and energy consumption to detect potential failures before they occur.
Reduced Downtime
Maintenance is performed only when necessary, minimizing unnecessary shutdowns and optimizing productivity.
Cost Savings
Facilities spend less on emergency repairs, unnecessary part replacements, and unplanned labor.
Extended Equipment Lifespan
Addressing minor issues before they escalate prevents excessive wear and tear.
Data-Driven Decision-Making
Analytics provide actionable insights, helping facility managers make informed maintenance choices.
Why Preventive Maintenance is the Old Way
The primary limitation of preventive maintenance is its reactive nature. Even though it schedules maintenance before failures occur, it doesn’t address equipment conditions in real-time. This can result in over-maintenance (servicing equipment too early) or under-maintenance (missing failures that occur between scheduled inspections). Predictive maintenance eliminates this inefficiency by continuously monitoring asset performance and alerting facility managers to potential issues before they disrupt operations.
Comparison: Preventive vs. Predictive Maintenance
Feature | Preventive Maintenance | Predictive Maintenance |
---|---|---|
Approach | Scheduled, time-based | Condition-based, real-time |
Downtime | Possible, due to unnecessary maintenance | Minimized, only when needed |
Costs | Higher, due to labor and material waste | Lower, optimized for efficiency |
Equipment Lifespan | Moderate improvement | Significantly extended |
Data Utilization | Limited, based on past performance | Advanced, using real-time analytics |
Implementing Predictive Maintenance in Facility Management
Shifting from preventive to predictive maintenance requires integrating smart technologies into facility operations. Here’s how to make the transition:
Deploy IoT Sensors
Install sensors on critical assets to monitor vibration, temperature, energy usage, and more.
Use AI and Machine Learning
Analyze data patterns to identify early warning signs of potential failures.
Leverage CMMS Software
A Computerized Maintenance Management System (CMMS) can track maintenance history, issue alerts, and optimize servicing schedules.
Train Maintenance Teams
Ensure staff understands predictive maintenance tools and can act on real-time insights.
Continuously Optimize
Regularly refine predictive maintenance strategies based on performance data.
The Future of Facility Maintenance
Facility managers can no longer afford to rely solely on outdated maintenance methods. Predictive maintenance is the future—offering smarter, more efficient, and cost-effective asset management. By adopting predictive maintenance, facilities can reduce downtime, cut operational costs, and ensure long-term reliability.
Ready to Upgrade Your Facility Maintenance Strategy?
Volta Insite specializes in predictive maintenance solutions tailored for modern facility management. Contact us today to learn how we can help you transition from outdated preventive maintenance to a cutting-edge predictive maintenance approach that maximizes efficiency and minimizes costs.